सेमीकंडक्टर उत्पादन प्रक्रियेतील एक महत्त्वाचा टप्पा म्हणून वेफर डायसिंग तंत्रज्ञान थेट चिप कामगिरी, उत्पन्न आणि उत्पादन खर्चाशी जोडलेले आहे.
#०१ वेफर डायसिंगची पार्श्वभूमी आणि महत्त्व
१.१ वेफर डायसिंगची व्याख्या
वेफर डायसिंग (ज्याला स्क्राइबिंग असेही म्हणतात) हे सेमीकंडक्टर उत्पादनातील एक आवश्यक पाऊल आहे, ज्याचा उद्देश प्रक्रिया केलेल्या वेफर्सना अनेक वैयक्तिक डायमध्ये विभाजित करणे आहे. या डायमध्ये सामान्यतः संपूर्ण सर्किट कार्यक्षमता असते आणि ते शेवटी इलेक्ट्रॉनिक उपकरणांच्या उत्पादनात वापरले जाणारे मुख्य घटक असतात. चिप डिझाइन अधिक जटिल होत असताना आणि परिमाण कमी होत असताना, वेफर डायसिंग तंत्रज्ञानासाठी अचूकता आणि कार्यक्षमता आवश्यकता अधिकाधिक कठोर होत आहेत.
व्यावहारिक ऑपरेशन्समध्ये, वेफर डायसिंगमध्ये सामान्यतः डायमंड ब्लेडसारख्या उच्च-परिशुद्धता साधनांचा वापर केला जातो जेणेकरून प्रत्येक डाय अबाधित आणि पूर्णपणे कार्यरत राहील याची खात्री होईल. प्रमुख पायऱ्यांमध्ये कापण्यापूर्वी तयारी, कापण्याच्या प्रक्रियेदरम्यान अचूक नियंत्रण आणि कापल्यानंतर गुणवत्ता तपासणी यांचा समावेश आहे.
कापण्यापूर्वी, अचूक कटिंग मार्ग सुनिश्चित करण्यासाठी वेफर चिन्हांकित आणि स्थित करणे आवश्यक आहे. कटिंग दरम्यान, वेफरला नुकसान टाळण्यासाठी टूल प्रेशर आणि वेग यासारखे पॅरामीटर्स काटेकोरपणे नियंत्रित केले पाहिजेत. कापल्यानंतर, प्रत्येक चिप कामगिरी मानके पूर्ण करते याची खात्री करण्यासाठी व्यापक गुणवत्ता तपासणी केली जाते.
वेफर डायसिंग तंत्रज्ञानाच्या मूलभूत तत्त्वांमध्ये केवळ कटिंग उपकरणांची निवड आणि प्रक्रिया पॅरामीटर्सची सेटिंगच नाही तर कटिंग गुणवत्तेवर सामग्रीच्या यांत्रिक गुणधर्मांचा आणि वैशिष्ट्यांचा प्रभाव देखील समाविष्ट आहे. उदाहरणार्थ, कमी-के डायलेक्ट्रिक सिलिकॉन वेफर्स, त्यांच्या निकृष्ट यांत्रिक गुणधर्मांमुळे, कटिंग दरम्यान ताण एकाग्रतेसाठी अत्यंत संवेदनशील असतात, ज्यामुळे चिपिंग आणि क्रॅकिंग सारख्या अपयश येतात. कमी-के मटेरियलची कमी कडकपणा आणि ठिसूळपणा त्यांना यांत्रिक शक्ती किंवा थर्मल ताणाखाली, विशेषतः कटिंग दरम्यान संरचनात्मक नुकसानास अधिक प्रवण बनवते. उच्च तापमानासह, साधन आणि वेफर पृष्ठभाग यांच्यातील संपर्कामुळे ताण एकाग्रता आणखी वाढू शकते.
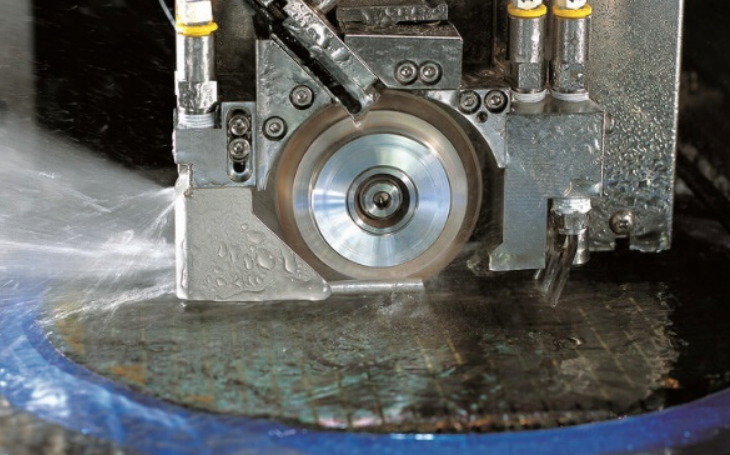
भौतिक विज्ञानातील प्रगतीसह, वेफर डायसिंग तंत्रज्ञान पारंपारिक सिलिकॉन-आधारित सेमीकंडक्टरच्या पलीकडे विस्तारले आहे ज्यामध्ये गॅलियम नायट्राइड (GaN) सारख्या नवीन सामग्रीचा समावेश आहे. हे नवीन साहित्य, त्यांच्या कडकपणा आणि संरचनात्मक गुणधर्मांमुळे, डायसिंग प्रक्रियेसाठी नवीन आव्हाने निर्माण करतात, ज्यासाठी कटिंग टूल्स आणि तंत्रांमध्ये आणखी सुधारणा आवश्यक आहेत.
सेमीकंडक्टर उद्योगातील एक महत्त्वाची प्रक्रिया म्हणून, वेफर डायसिंगला विकसित होत असलेल्या मागण्या आणि तांत्रिक प्रगतीनुसार ऑप्टिमाइझ केले जात आहे, ज्यामुळे भविष्यातील मायक्रोइलेक्ट्रॉनिक्स आणि इंटिग्रेटेड सर्किट तंत्रज्ञानाचा पाया रचला जात आहे.
वेफर डायसिंग तंत्रज्ञानातील सुधारणा सहाय्यक साहित्य आणि साधनांच्या विकासापलीकडे जातात. त्यामध्ये प्रक्रिया ऑप्टिमायझेशन, उपकरणांच्या कामगिरीत सुधारणा आणि डायसिंग पॅरामीटर्सचे अचूक नियंत्रण देखील समाविष्ट आहे. या प्रगतीचा उद्देश वेफर डायसिंग प्रक्रियेत उच्च अचूकता, कार्यक्षमता आणि स्थिरता सुनिश्चित करणे आहे, ज्यामुळे सेमीकंडक्टर उद्योगाची लहान परिमाणे, उच्च एकात्मता आणि अधिक जटिल चिप संरचनांची आवश्यकता पूर्ण होते.
सुधारणा क्षेत्र | विशिष्ट उपाययोजना | परिणाम |
प्रक्रिया ऑप्टिमायझेशन | - सुरुवातीच्या तयारींमध्ये सुधारणा करा, जसे की अधिक अचूक वेफर पोझिशनिंग आणि मार्ग नियोजन. | - कटिंग चुका कमी करा आणि स्थिरता सुधारा. |
- कटिंग चुका कमी करा आणि स्थिरता वाढवा. | - साधनांचा दाब, वेग आणि तापमान समायोजित करण्यासाठी रिअल-टाइम देखरेख आणि अभिप्राय यंत्रणा स्वीकारा. | |
- वेफर ब्रेकेज रेट कमी करा आणि चिपची गुणवत्ता सुधारा. | ||
उपकरणांची कार्यक्षमता वाढवणे | - उच्च-परिशुद्धता असलेल्या यांत्रिक प्रणाली आणि प्रगत ऑटोमेशन नियंत्रण तंत्रज्ञानाचा वापर करा. | - कटिंग अचूकता वाढवा आणि साहित्याचा अपव्यय कमी करा. |
- उच्च-कडकपणा असलेल्या मटेरियल वेफर्ससाठी योग्य लेसर कटिंग तंत्रज्ञान सादर करा. | - उत्पादन कार्यक्षमता सुधारा आणि मॅन्युअल चुका कमी करा. | |
- स्वयंचलित देखरेख आणि समायोजनासाठी उपकरणे ऑटोमेशन वाढवा. | ||
अचूक पॅरामीटर नियंत्रण | - कटिंग डेप्थ, स्पीड, टूल प्रकार आणि कूलिंग पद्धती यासारखे पॅरामीटर्स बारीक समायोजित करा. | - डाय अखंडता आणि विद्युत कार्यक्षमता सुनिश्चित करा. |
- वेफर मटेरियल, जाडी आणि रचनेनुसार पॅरामीटर्स कस्टमाइझ करा. | - उत्पादन दर वाढवा, साहित्याचा अपव्यय कमी करा आणि उत्पादन खर्च कमी करा. | |
धोरणात्मक महत्त्व | - बाजारातील मागण्या पूर्ण करण्यासाठी सतत नवीन तांत्रिक मार्गांचा शोध घ्या, प्रक्रिया ऑप्टिमाइझ करा आणि उपकरणांची क्षमता वाढवा. | - नवीन साहित्य आणि प्रगत चिप डिझाइनच्या विकासास समर्थन देऊन, चिप उत्पादन उत्पन्न आणि कामगिरी सुधारा. |
१.२ वेफर डायसिंगचे महत्त्व
अर्धवाहक उत्पादन प्रक्रियेत वेफर डायसिंग महत्त्वपूर्ण भूमिका बजावते, जे पुढील चरणांवर तसेच अंतिम उत्पादनाच्या गुणवत्तेवर आणि कामगिरीवर थेट परिणाम करते. त्याचे महत्त्व खालीलप्रमाणे तपशीलवार सांगता येईल:
प्रथम, चिप उत्पादन आणि विश्वासार्हता सुनिश्चित करण्यासाठी डायसिंगची अचूकता आणि सुसंगतता महत्त्वाची आहे. उत्पादनादरम्यान, वेफर्स अनेक प्रक्रिया चरणांमधून जातात जेणेकरून असंख्य गुंतागुंतीच्या सर्किट स्ट्रक्चर्स तयार होतात, ज्या वैयक्तिक चिप्स (डाय) मध्ये अचूकपणे विभागल्या पाहिजेत. डायसिंग प्रक्रियेदरम्यान अलाइनमेंट किंवा कटिंगमध्ये महत्त्वपूर्ण त्रुटी असल्यास, सर्किट्स खराब होऊ शकतात, ज्यामुळे चिपची कार्यक्षमता आणि विश्वासार्हता प्रभावित होते. म्हणूनच, उच्च-परिशुद्धता डायसिंग तंत्रज्ञान केवळ प्रत्येक चिपची अखंडता सुनिश्चित करत नाही तर अंतर्गत सर्किट्सचे नुकसान देखील टाळते, ज्यामुळे एकूण उत्पन्न दर सुधारतो.
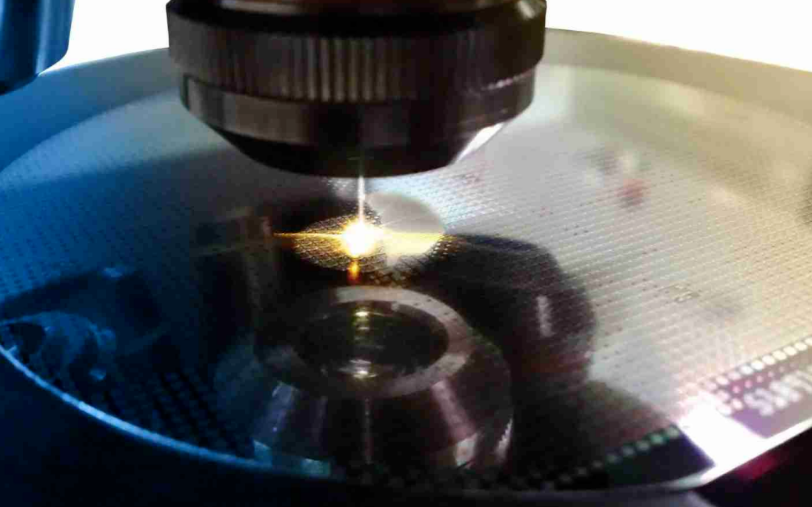
दुसरे म्हणजे, वेफर डायसिंगचा उत्पादन कार्यक्षमता आणि खर्च नियंत्रणावर लक्षणीय परिणाम होतो. उत्पादन प्रक्रियेतील एक महत्त्वाचा टप्पा म्हणून, त्याची कार्यक्षमता पुढील चरणांच्या प्रगतीवर थेट परिणाम करते. डायसिंग प्रक्रियेचे ऑप्टिमायझेशन करून, ऑटोमेशन पातळी वाढवून आणि कटिंग गती सुधारून, एकूण उत्पादन कार्यक्षमता मोठ्या प्रमाणात वाढवता येते.
दुसरीकडे, डाइसिंग दरम्यान होणारा साहित्याचा अपव्यय हा खर्च व्यवस्थापनात एक महत्त्वाचा घटक आहे. प्रगत डाइसिंग तंत्रज्ञानाचा वापर केल्याने कटिंग प्रक्रियेदरम्यान अनावश्यक साहित्याचे नुकसान कमी होतेच, शिवाय वेफरचा वापर देखील वाढतो, ज्यामुळे उत्पादन खर्च कमी होतो.
सेमीकंडक्टर तंत्रज्ञानातील प्रगतीसह, वेफर व्यास वाढत राहतात आणि त्यानुसार सर्किट घनता वाढते, ज्यामुळे डायसिंग तंत्रज्ञानावर जास्त मागणी होते. मोठ्या वेफर्सना कटिंग मार्गांचे अधिक अचूक नियंत्रण आवश्यक असते, विशेषतः उच्च-घनतेच्या सर्किट क्षेत्रांमध्ये, जिथे किरकोळ विचलन देखील अनेक चिप्स दोषपूर्ण बनवू शकतात. याव्यतिरिक्त, मोठ्या वेफर्समध्ये अधिक कटिंग लाईन्स आणि अधिक जटिल प्रक्रिया चरणांचा समावेश असतो, ज्यामुळे या आव्हानांना तोंड देण्यासाठी डायसिंग तंत्रज्ञानाच्या अचूकता, सुसंगतता आणि कार्यक्षमतेत आणखी सुधारणा आवश्यक असतात.
१.३ वेफर डायसिंग प्रक्रिया
वेफर डायसिंग प्रक्रियेमध्ये तयारीच्या टप्प्यापासून ते अंतिम गुणवत्ता तपासणीपर्यंतचे सर्व टप्पे समाविष्ट आहेत, प्रत्येक टप्पा चिप्सची गुणवत्ता आणि कामगिरी सुनिश्चित करण्यासाठी महत्त्वाचा आहे. खाली प्रत्येक टप्प्याचे तपशीलवार स्पष्टीकरण दिले आहे.
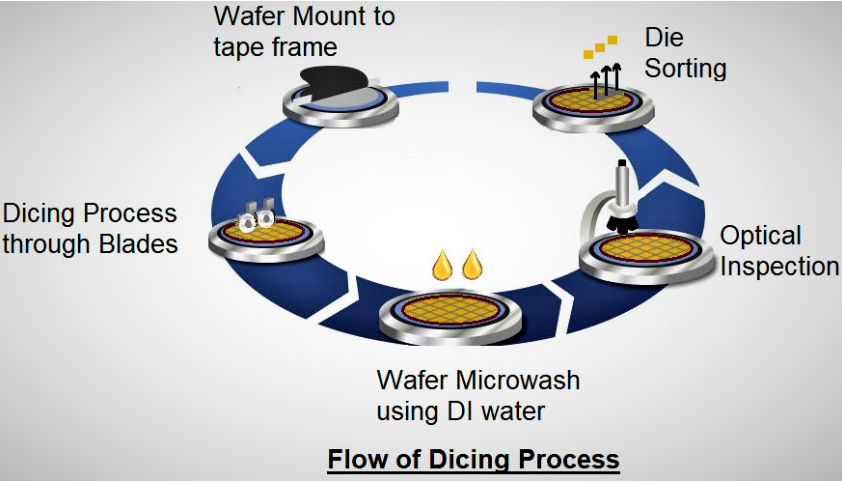
टप्पा | तपशीलवार वर्णन |
तयारीचा टप्पा | -वेफर साफसफाई: स्वच्छ पृष्ठभाग सुनिश्चित करण्यासाठी, अशुद्धता, कण आणि दूषित पदार्थ काढून टाकण्यासाठी उच्च-शुद्धता असलेले पाणी आणि विशेष स्वच्छता एजंट्स, अल्ट्रासोनिक किंवा यांत्रिक स्क्रबिंगसह एकत्रितपणे वापरा. -अचूक स्थिती: डिझाइन केलेल्या कटिंग मार्गांवर वेफर अचूकपणे विभागले गेले आहे याची खात्री करण्यासाठी उच्च-परिशुद्धता उपकरणे वापरा. -वेफर फिक्सेशन: कटिंग दरम्यान स्थिरता राखण्यासाठी, कंपन किंवा हालचालीमुळे होणारे नुकसान टाळण्यासाठी वेफरला टेप फ्रेमवर सुरक्षित करा. |
कटिंग टप्पा | -ब्लेड डायसिंग: सिलिकॉन-आधारित सामग्रीसाठी योग्य आणि किफायतशीर, भौतिक कटिंगसाठी हाय-स्पीड फिरणारे डायमंड-लेपित ब्लेड वापरा. -लेसर डायसिंग: संपर्क नसलेल्या कटिंगसाठी उच्च-ऊर्जा लेसर बीम वापरा, जे गॅलियम नायट्राइड सारख्या ठिसूळ किंवा उच्च-कडकपणाच्या सामग्रीसाठी आदर्श आहे, उच्च अचूकता आणि कमी सामग्रीचे नुकसान देते. -नवीन तंत्रज्ञान: उष्णता-प्रभावित क्षेत्रे कमीत कमी करून कार्यक्षमता आणि अचूकता सुधारण्यासाठी लेसर आणि प्लाझ्मा कटिंग तंत्रज्ञानाचा परिचय द्या. |
स्वच्छता टप्पा | - कटिंग दरम्यान निर्माण होणारा कचरा आणि धूळ काढून टाकण्यासाठी, त्यानंतरच्या प्रक्रियांवर किंवा चिप इलेक्ट्रिकल कार्यक्षमतेवर परिणाम होण्यापासून अवशेषांना प्रतिबंधित करण्यासाठी, अल्ट्रासोनिक किंवा स्प्रे क्लीनिंगसह डीआयोनाइज्ड वॉटर (डीआय वॉटर) आणि विशेष क्लिनिंग एजंट्स वापरा. - उच्च-शुद्धता असलेले DI पाणी नवीन दूषित घटकांना आत येण्यापासून रोखते, ज्यामुळे स्वच्छ वेफर वातावरण सुनिश्चित होते. |
तपासणी टप्पा | -ऑप्टिकल तपासणी: दोषांची जलद ओळख पटविण्यासाठी, चिप्समध्ये क्रॅक किंवा चिप्स नसल्याची खात्री करण्यासाठी, तपासणी कार्यक्षमता सुधारण्यासाठी आणि मानवी त्रुटी कमी करण्यासाठी एआय अल्गोरिदमसह एकत्रित ऑप्टिकल डिटेक्शन सिस्टम वापरा. -परिमाण मापन: चिपचे परिमाण डिझाइनच्या वैशिष्ट्यांशी जुळतात का ते तपासा. -विद्युत कामगिरी चाचणी: क्रिटिकल चिप्सची इलेक्ट्रिकल कामगिरी मानकांची पूर्तता करते याची खात्री करा, त्यानंतरच्या अनुप्रयोगांमध्ये विश्वासार्हतेची हमी द्या. |
वर्गीकरण टप्पा | - टेप फ्रेममधून पात्र चिप्स वेगळे करण्यासाठी रोबोटिक आर्म्स किंवा व्हॅक्यूम सक्शन कप वापरा आणि कामगिरीनुसार त्यांना स्वयंचलितपणे क्रमवारी लावा, उत्पादन कार्यक्षमता आणि लवचिकता सुनिश्चित करा आणि अचूकता सुधारा. |
वेफर कटिंग प्रक्रियेमध्ये वेफर क्लीनिंग, पोझिशनिंग, कटिंग, क्लीनिंग, इन्स्पेक्शन आणि सॉर्टिंग यांचा समावेश असतो, ज्यामध्ये प्रत्येक टप्पा महत्त्वाचा असतो. ऑटोमेशन, लेसर कटिंग आणि एआय इन्स्पेक्शन तंत्रज्ञानातील प्रगतीमुळे, आधुनिक वेफर कटिंग सिस्टम उच्च अचूकता, वेग आणि कमी मटेरियल लॉस साध्य करू शकतात. भविष्यात, लेसर आणि प्लाझ्मा सारख्या नवीन कटिंग तंत्रज्ञान हळूहळू वाढत्या जटिल चिप डिझाइनच्या गरजा पूर्ण करण्यासाठी पारंपारिक ब्लेड कटिंगची जागा घेतील, ज्यामुळे सेमीकंडक्टर मॅन्युफॅक्चरिंग प्रक्रियेचा विकास आणखी वाढेल.
वेफर कटिंग तंत्रज्ञान आणि त्याची तत्त्वे
ही प्रतिमा तीन सामान्य वेफर कटिंग तंत्रज्ञान दर्शवते:ब्लेड डायसिंग,लेसर डायसिंग, आणिप्लाझ्मा डायसिंग. खाली या तीन तंत्रांचे तपशीलवार विश्लेषण आणि पूरक स्पष्टीकरण दिले आहे:
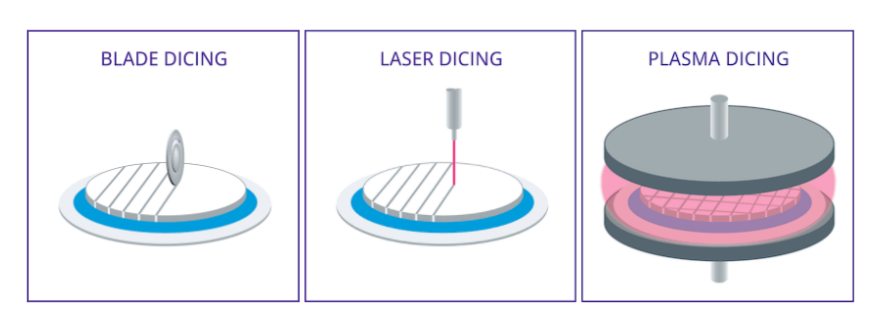
सेमीकंडक्टर मॅन्युफॅक्चरिंगमध्ये, वेफर कटिंग ही एक महत्त्वाची पायरी आहे ज्यासाठी वेफरच्या जाडीवर आधारित योग्य कटिंग पद्धत निवडणे आवश्यक आहे. पहिले पाऊल म्हणजे वेफरची जाडी निश्चित करणे. जर वेफरची जाडी १०० मायक्रॉनपेक्षा जास्त असेल, तर ब्लेड डायसिंग ही कटिंग पद्धत म्हणून निवडली जाऊ शकते. जर ब्लेड डायसिंग योग्य नसेल, तर फ्रॅक्चर डायसिंग पद्धत वापरली जाऊ शकते, ज्यामध्ये स्क्राइब कटिंग आणि ब्लेड डायसिंग तंत्र दोन्ही समाविष्ट आहेत.
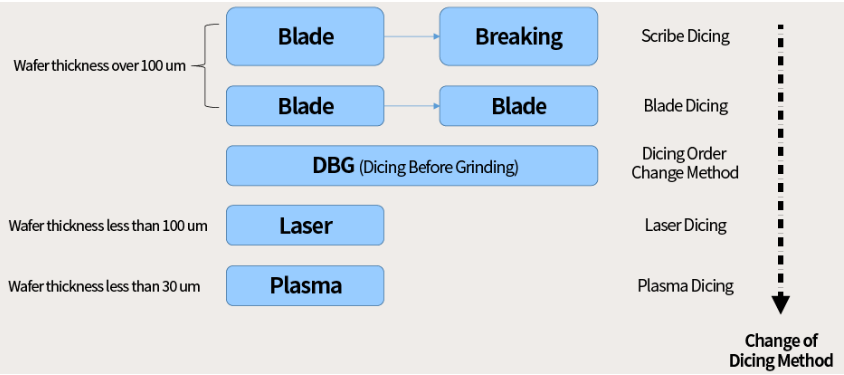
जेव्हा वेफरची जाडी ३० ते १०० मायक्रॉन दरम्यान असते, तेव्हा डीबीजी (ग्राइंडिंग करण्यापूर्वी डाइस) पद्धत वापरण्याची शिफारस केली जाते. या प्रकरणात, सर्वोत्तम परिणाम साध्य करण्यासाठी स्क्राइब कटिंग, ब्लेड डायसिंग किंवा आवश्यकतेनुसार कटिंग क्रम समायोजित करणे निवडले जाऊ शकते.
३० मायक्रॉनपेक्षा कमी जाडी असलेल्या अति-पातळ वेफर्ससाठी, जास्त नुकसान न करता पातळ वेफर्स अचूकपणे कापण्याची क्षमता असल्यामुळे लेसर कटिंग ही पसंतीची पद्धत बनते. जर लेसर कटिंग विशिष्ट आवश्यकता पूर्ण करू शकत नसेल, तर प्लाझ्मा कटिंगचा पर्याय म्हणून वापर केला जाऊ शकतो. वेगवेगळ्या जाडीच्या परिस्थितीत सर्वात योग्य वेफर कटिंग तंत्रज्ञान निवडले जाईल याची खात्री करण्यासाठी हा फ्लोचार्ट एक स्पष्ट निर्णय घेण्याचा मार्ग प्रदान करतो.
२.१ यांत्रिक कटिंग तंत्रज्ञान
वेफर डायसिंगमध्ये यांत्रिक कटिंग तंत्रज्ञान ही पारंपारिक पद्धत आहे. वेफर कापण्यासाठी कटिंग टूल म्हणून हाय-स्पीड रोटेटिंग डायमंड ग्राइंडिंग व्हील वापरणे हे मुख्य तत्व आहे. मुख्य उपकरणांमध्ये एअर-बेअरिंग स्पिंडल समाविष्ट आहे, जे डायमंड ग्राइंडिंग व्हील टूलला उच्च वेगाने चालवते जेणेकरून पूर्वनिर्धारित कटिंग मार्गावर अचूक कटिंग किंवा ग्रूव्हिंग करता येईल. कमी किमतीत, उच्च कार्यक्षमता आणि व्यापक वापरामुळे हे तंत्रज्ञान उद्योगात मोठ्या प्रमाणावर वापरले जाते.
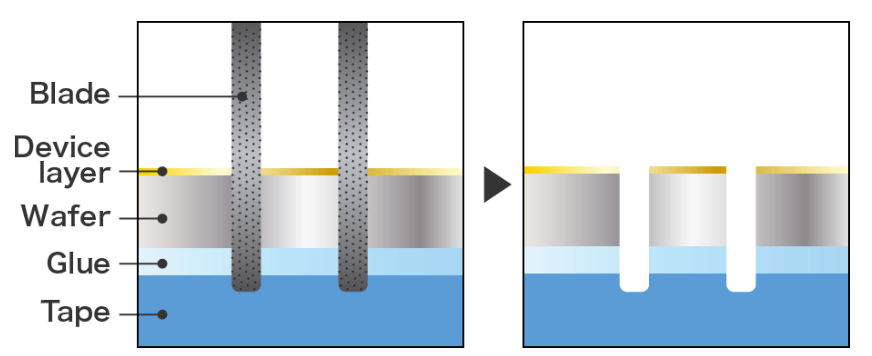
फायदे
डायमंड ग्राइंडिंग व्हील टूल्सची उच्च कडकपणा आणि वेअर रेझिस्टन्स यांत्रिक कटिंग तंत्रज्ञानाला विविध वेफर मटेरियलच्या कटिंग गरजांशी जुळवून घेण्यास सक्षम करते, मग ते पारंपारिक सिलिकॉन-आधारित मटेरियल असोत किंवा नवीन कंपाऊंड सेमीकंडक्टर असोत. त्याचे ऑपरेशन सोपे आहे, तुलनेने कमी तांत्रिक आवश्यकतांसह, मोठ्या प्रमाणात उत्पादनात त्याची लोकप्रियता वाढवते. याव्यतिरिक्त, लेसर कटिंगसारख्या इतर कटिंग पद्धतींच्या तुलनेत, यांत्रिक कटिंगचा खर्च अधिक नियंत्रित करण्यायोग्य आहे, ज्यामुळे ते मोठ्या प्रमाणात उत्पादन गरजांसाठी योग्य बनते.
मर्यादा
असंख्य फायदे असूनही, यांत्रिक कटिंग तंत्रज्ञानालाही मर्यादा आहेत. पहिले म्हणजे, टूल आणि वेफरमधील भौतिक संपर्कामुळे, कटिंगची अचूकता तुलनेने मर्यादित असते, ज्यामुळे अनेकदा मितीय विचलन होते जे नंतरच्या चिप पॅकेजिंग आणि चाचणीच्या अचूकतेवर परिणाम करू शकते. दुसरे म्हणजे, यांत्रिक कटिंग प्रक्रियेदरम्यान चिपिंग आणि क्रॅकसारखे दोष सहजपणे उद्भवू शकतात, जे केवळ उत्पादन दरावर परिणाम करत नाहीत तर चिप्सच्या विश्वासार्हतेवर आणि आयुष्यमानावर देखील नकारात्मक परिणाम करू शकतात. यांत्रिक ताणामुळे होणारे नुकसान उच्च-घनतेच्या चिप उत्पादनासाठी विशेषतः हानिकारक आहे, विशेषतः ठिसूळ साहित्य कापताना, जिथे या समस्या अधिक प्रमुख असतात.
तांत्रिक सुधारणा
या मर्यादांवर मात करण्यासाठी, संशोधक यांत्रिक कटिंग प्रक्रियेला सतत अनुकूलित करत आहेत. कटिंगची अचूकता आणि टिकाऊपणा सुधारण्यासाठी ग्राइंडिंग व्हील्सची रचना आणि मटेरियल निवड वाढवणे हे प्रमुख सुधारणा आहेत. याव्यतिरिक्त, कटिंग उपकरणांच्या स्ट्रक्चरल डिझाइन आणि नियंत्रण प्रणालींचे ऑप्टिमाइझिंग केल्याने कटिंग प्रक्रियेची स्थिरता आणि ऑटोमेशन आणखी सुधारले आहे. या प्रगतीमुळे मानवी ऑपरेशन्समुळे होणाऱ्या चुका कमी होतात आणि कट्सची सुसंगतता सुधारते. कटिंग प्रक्रियेदरम्यान विसंगतींचे रिअल-टाइम निरीक्षण करण्यासाठी प्रगत तपासणी आणि गुणवत्ता नियंत्रण तंत्रज्ञानाचा परिचय करून दिल्याने कटिंगची विश्वासार्हता आणि उत्पन्नातही लक्षणीय सुधारणा झाली आहे.
भविष्यातील विकास आणि नवीन तंत्रज्ञान
वेफर कटिंगमध्ये मेकॅनिकल कटिंग तंत्रज्ञानाचे अजूनही महत्त्वपूर्ण स्थान असले तरी, सेमीकंडक्टर प्रक्रिया विकसित होताना नवीन कटिंग तंत्रज्ञान वेगाने प्रगती करत आहेत. उदाहरणार्थ, थर्मल लेसर कटिंग तंत्रज्ञानाचा वापर मेकॅनिकल कटिंगमधील अचूकता आणि दोष समस्यांवर नवीन उपाय प्रदान करतो. ही संपर्क नसलेली कटिंग पद्धत वेफरवरील भौतिक ताण कमी करते, चिपिंग आणि क्रॅकिंगच्या घटनांमध्ये लक्षणीयरीत्या घट करते, विशेषतः अधिक ठिसूळ पदार्थ कापताना. भविष्यात, उदयोन्मुख कटिंग तंत्रांसह मेकॅनिकल कटिंग तंत्रज्ञानाचे एकत्रीकरण सेमीकंडक्टर उत्पादनास अधिक पर्याय आणि लवचिकता प्रदान करेल, उत्पादन कार्यक्षमता आणि चिप गुणवत्ता आणखी वाढवेल.
शेवटी, जरी यांत्रिक कटिंग तंत्रज्ञानात काही तोटे असले तरी, सतत तांत्रिक सुधारणा आणि नवीन कटिंग तंत्रांसह त्याचे एकत्रीकरण यामुळे ते सेमीकंडक्टर उत्पादनात महत्त्वाची भूमिका बजावू शकते आणि भविष्यातील प्रक्रियांमध्ये त्याची स्पर्धात्मकता टिकवून ठेवू शकते.
२.२ लेसर कटिंग तंत्रज्ञान
वेफर कटिंगमध्ये एक नवीन पद्धत म्हणून लेसर कटिंग तंत्रज्ञानाने हळूहळू सेमीकंडक्टर उद्योगात व्यापक लक्ष वेधले आहे कारण त्याची उच्च अचूकता, यांत्रिक संपर्क नुकसानाचा अभाव आणि जलद कटिंग क्षमता. हे तंत्रज्ञान वेफर मटेरियलच्या पृष्ठभागावर एक लहान उष्णता-प्रभावित झोन तयार करण्यासाठी लेसर बीमची उच्च ऊर्जा घनता आणि फोकसिंग क्षमता वापरते. जेव्हा लेसर बीम वेफरवर लावला जातो तेव्हा निर्माण होणारा थर्मल स्ट्रेस मटेरियलला नियुक्त केलेल्या ठिकाणी फ्रॅक्चर करतो, ज्यामुळे अचूक कटिंग साध्य होते.
लेसर कटिंग तंत्रज्ञानाचे फायदे
• उच्च अचूकता: लेसर बीमची अचूक स्थिती निश्चित करण्याची क्षमता मायक्रॉन किंवा अगदी नॅनोमीटर-स्तरीय कटिंग अचूकता प्रदान करते, जे आधुनिक उच्च-परिशुद्धता, उच्च-घनता एकात्मिक सर्किट उत्पादनाच्या आवश्यकता पूर्ण करते.
• यांत्रिक संपर्क नाही: लेसर कटिंगमुळे वेफरशी शारीरिक संपर्क टाळता येतो, यांत्रिक कटिंगमधील सामान्य समस्या जसे की चिपिंग आणि क्रॅकिंग टाळता येते, ज्यामुळे चिप्सचा उत्पादन दर आणि विश्वासार्हता लक्षणीयरीत्या सुधारते.
• जलद कटिंग गती: लेसर कटिंगचा उच्च वेग उत्पादन कार्यक्षमता वाढविण्यास हातभार लावतो, ज्यामुळे ते मोठ्या प्रमाणात, उच्च-गती उत्पादन परिस्थितींसाठी विशेषतः योग्य बनते.
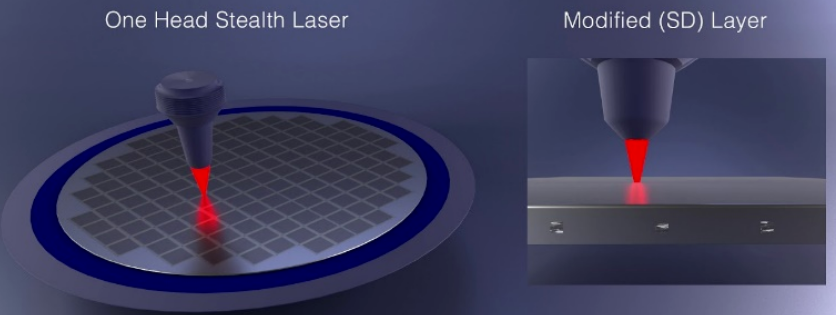
आव्हाने
• उच्च उपकरणांचा खर्च: लेसर कटिंग उपकरणांसाठी सुरुवातीची गुंतवणूक जास्त असते, जी आर्थिक दबाव निर्माण करते, विशेषतः लहान ते मध्यम आकाराच्या उत्पादन उद्योगांसाठी.
• जटिल प्रक्रिया नियंत्रण: लेसर कटिंगसाठी ऊर्जा घनता, फोकस स्थिती आणि कटिंग गती यासह अनेक पॅरामीटर्सचे अचूक नियंत्रण आवश्यक असते, ज्यामुळे प्रक्रिया गुंतागुंतीची होते.
• उष्णतेमुळे प्रभावित क्षेत्राच्या समस्या: लेसर कटिंगच्या संपर्करहित स्वरूपामुळे यांत्रिक नुकसान कमी होते, परंतु उष्णता-प्रभावित झोन (HAZ) मुळे होणारा थर्मल ताण वेफर मटेरियलच्या गुणधर्मांवर नकारात्मक परिणाम करू शकतो. हा परिणाम कमी करण्यासाठी प्रक्रियेचे पुढील ऑप्टिमायझेशन आवश्यक आहे.
तांत्रिक सुधारणा दिशानिर्देश
या आव्हानांना तोंड देण्यासाठी, संशोधक उपकरणांचा खर्च कमी करण्यावर, कटिंग कार्यक्षमता सुधारण्यावर आणि प्रक्रिया प्रवाह अनुकूल करण्यावर लक्ष केंद्रित करत आहेत.
• कार्यक्षम लेसर आणि ऑप्टिकल सिस्टम्स: अधिक कार्यक्षम लेसर आणि प्रगत ऑप्टिकल प्रणाली विकसित करून, कटिंगची अचूकता आणि वेग वाढवताना उपकरणांचा खर्च कमी करणे शक्य आहे.
• प्रक्रिया पॅरामीटर्स ऑप्टिमायझ करणे: उष्णतेमुळे प्रभावित क्षेत्र कमी करणाऱ्या प्रक्रिया सुधारण्यासाठी लेसर आणि वेफर मटेरियलमधील परस्परसंवादावर सखोल संशोधन केले जात आहे, ज्यामुळे कटिंगची गुणवत्ता सुधारते.
• बुद्धिमान नियंत्रण प्रणाली: बुद्धिमान नियंत्रण तंत्रज्ञानाच्या विकासाचा उद्देश लेसर कटिंग प्रक्रिया स्वयंचलित आणि ऑप्टिमाइझ करणे, तिची स्थिरता आणि सुसंगतता सुधारणे आहे.
लेसर कटिंग तंत्रज्ञान विशेषतः अल्ट्रा-थिन वेफर्स आणि उच्च-परिशुद्धता कटिंग परिस्थितींमध्ये प्रभावी आहे. वेफरचा आकार वाढत असताना आणि सर्किट घनता वाढत असताना, पारंपारिक यांत्रिक कटिंग पद्धती आधुनिक सेमीकंडक्टर उत्पादनाच्या उच्च-परिशुद्धता आणि उच्च-कार्यक्षमतेच्या मागण्या पूर्ण करण्यासाठी संघर्ष करतात. त्याच्या अद्वितीय फायद्यांमुळे, लेसर कटिंग या क्षेत्रांमध्ये पसंतीचा उपाय बनत आहे.
जरी लेसर कटिंग तंत्रज्ञानासमोर अजूनही उच्च उपकरणांचा खर्च आणि प्रक्रिया जटिलता यासारख्या आव्हानांचा सामना करावा लागत असला तरी, उच्च अचूकता आणि संपर्क नसलेल्या नुकसानीमधील त्याचे अद्वितीय फायदे सेमीकंडक्टर उत्पादनात विकासासाठी एक महत्त्वाची दिशा बनवतात. लेसर तंत्रज्ञान आणि बुद्धिमान नियंत्रण प्रणाली प्रगती करत असताना, लेसर कटिंगमुळे वेफर कटिंग कार्यक्षमता आणि गुणवत्ता आणखी सुधारण्याची अपेक्षा आहे, ज्यामुळे सेमीकंडक्टर उद्योगाचा सतत विकास होईल.
२.३ प्लाझ्मा कटिंग तंत्रज्ञान
अलिकडच्या वर्षांत, एक उदयोन्मुख वेफर डायसिंग पद्धत म्हणून प्लाझ्मा कटिंग तंत्रज्ञानाने लक्षणीय लक्ष वेधले आहे. हे तंत्रज्ञान प्लाझ्मा बीमची ऊर्जा, वेग आणि कटिंग मार्ग नियंत्रित करून वेफर्स अचूकपणे कापण्यासाठी उच्च-ऊर्जा प्लाझ्मा बीम वापरते, ज्यामुळे इष्टतम कटिंग परिणाम प्राप्त होतात.
कामाचे तत्व आणि फायदे
प्लाझ्मा कटिंगची प्रक्रिया उपकरणांद्वारे निर्माण होणाऱ्या उच्च-तापमान, उच्च-ऊर्जा प्लाझ्मा बीमवर अवलंबून असते. हे बीम वेफर मटेरियलला त्याच्या वितळण्याच्या किंवा बाष्पीभवन बिंदूपर्यंत खूप कमी वेळात गरम करू शकते, ज्यामुळे जलद कटिंग शक्य होते. पारंपारिक यांत्रिक किंवा लेसर कटिंगच्या तुलनेत, प्लाझ्मा कटिंग जलद आहे आणि एक लहान उष्णता-प्रभावित झोन तयार करते, ज्यामुळे कटिंग दरम्यान क्रॅक आणि नुकसान होण्याची शक्यता प्रभावीपणे कमी होते.
व्यावहारिक अनुप्रयोगांमध्ये, प्लाझ्मा कटिंग तंत्रज्ञान विशेषतः जटिल आकारांसह वेफर्स हाताळण्यात पारंगत आहे. त्याचा उच्च-ऊर्जा, समायोज्य प्लाझ्मा बीम उच्च अचूकतेसह अनियमित आकाराचे वेफर्स सहजपणे कापू शकतो. म्हणूनच, मायक्रोइलेक्ट्रॉनिक्स उत्पादनात, विशेषतः उच्च-स्तरीय चिप्सच्या कस्टमाइज्ड आणि लहान-बॅच उत्पादनात, हे तंत्रज्ञान व्यापक वापरासाठी उत्तम आशा दर्शवते.
आव्हाने आणि मर्यादा
प्लाझ्मा कटिंग तंत्रज्ञानाचे अनेक फायदे असूनही, त्यात काही आव्हाने देखील आहेत.
• गुंतागुंतीची प्रक्रिया: प्लाझ्मा कटिंग प्रक्रिया गुंतागुंतीची आहे आणि त्यासाठी उच्च-परिशुद्धता उपकरणे आणि अनुभवी ऑपरेटरची आवश्यकता असतेकटिंगमध्ये अचूकता आणि स्थिरता.
• पर्यावरण नियंत्रण आणि सुरक्षितता: प्लाझ्मा बीमच्या उच्च-तापमान, उच्च-ऊर्जा स्वरूपासाठी कठोर पर्यावरणीय नियंत्रण आणि सुरक्षा उपायांची आवश्यकता असते, ज्यामुळे अंमलबजावणीची जटिलता आणि खर्च वाढतो.
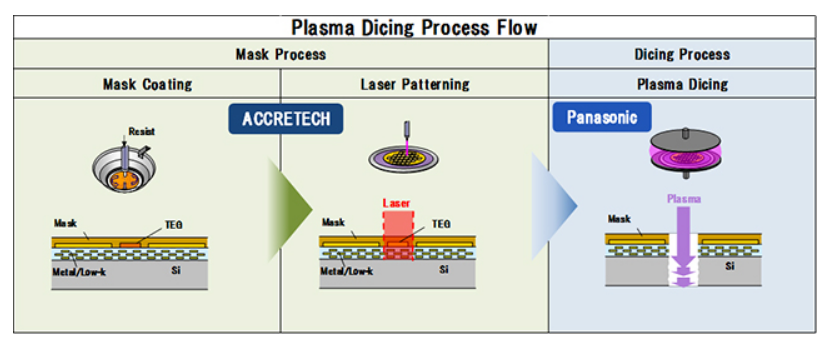
भविष्यातील विकासाच्या दिशानिर्देश
तांत्रिक प्रगतीसह, प्लाझ्मा कटिंगशी संबंधित आव्हाने हळूहळू दूर होण्याची अपेक्षा आहे. अधिक स्मार्ट आणि अधिक स्थिर कटिंग उपकरणे विकसित करून, मॅन्युअल ऑपरेशन्सवरील अवलंबित्व कमी केले जाऊ शकते, ज्यामुळे उत्पादन कार्यक्षमता सुधारते. त्याच वेळी, प्रक्रिया पॅरामीटर्स आणि कटिंग वातावरणाचे अनुकूलन केल्याने सुरक्षा धोके आणि ऑपरेशनल खर्च कमी होण्यास मदत होईल.
सेमीकंडक्टर उद्योगात, वेफर कटिंग आणि डायसिंग तंत्रज्ञानातील नवोपक्रम उद्योगाच्या विकासाला चालना देण्यासाठी महत्त्वाचे आहेत. उच्च अचूकता, कार्यक्षमता आणि जटिल वेफर आकार हाताळण्याची क्षमता असलेले प्लाझ्मा कटिंग तंत्रज्ञान या क्षेत्रात एक महत्त्वाचा नवीन खेळाडू म्हणून उदयास आले आहे. जरी काही आव्हाने अजूनही आहेत, तरी या समस्या हळूहळू सतत तांत्रिक नवोपक्रमाने सोडवल्या जातील, ज्यामुळे सेमीकंडक्टर उत्पादनात अधिक शक्यता आणि संधी येतील.
प्लाझ्मा कटिंग तंत्रज्ञानाच्या वापराच्या शक्यता खूप मोठ्या आहेत आणि भविष्यात ते सेमीकंडक्टर उत्पादनात अधिक महत्त्वाची भूमिका बजावेल अशी अपेक्षा आहे. सतत तांत्रिक नवोपक्रम आणि ऑप्टिमायझेशनद्वारे, प्लाझ्मा कटिंग केवळ विद्यमान आव्हानांना तोंड देणार नाही तर सेमीकंडक्टर उद्योगाच्या वाढीचा एक शक्तिशाली चालक देखील बनेल.
२.४ गुणवत्ता कमी करणे आणि प्रभावित करणारे घटक
त्यानंतरच्या चिप पॅकेजिंग, चाचणी आणि अंतिम उत्पादनाची एकूण कामगिरी आणि विश्वासार्हता यासाठी वेफर कटिंगची गुणवत्ता महत्त्वाची आहे. कटिंग दरम्यान येणाऱ्या सामान्य समस्यांमध्ये क्रॅक, चिपिंग आणि कटिंगमधील विचलन यांचा समावेश होतो. या समस्या एकत्रितपणे काम करणाऱ्या अनेक घटकांमुळे प्रभावित होतात.
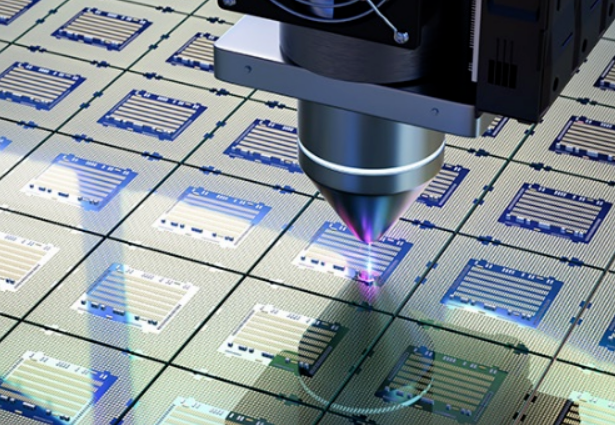
श्रेणी | सामग्री | प्रभाव |
प्रक्रिया पॅरामीटर्स | कटिंगचा वेग, फीड रेट आणि कटिंगची खोली कटिंग प्रक्रियेच्या स्थिरतेवर आणि अचूकतेवर थेट परिणाम करते. चुकीच्या सेटिंग्जमुळे ताण एकाग्रता आणि जास्त उष्णता-प्रभावित झोन होऊ शकतो, ज्यामुळे क्रॅक आणि चिप्स होऊ शकतात. वेफर मटेरियल, जाडी आणि कटिंग आवश्यकतांवर आधारित पॅरामीटर्स योग्यरित्या समायोजित करणे हे इच्छित कटिंग परिणाम साध्य करण्यासाठी महत्त्वाचे आहे. | योग्य प्रक्रिया पॅरामीटर्स अचूक कटिंग सुनिश्चित करतात आणि क्रॅक आणि चिप्स सारख्या दोषांचा धोका कमी करतात. |
उपकरणे आणि साहित्य घटक | -ब्लेडची गुणवत्ता: ब्लेडचे मटेरियल, कडकपणा आणि झीज प्रतिरोधकता कटिंग प्रक्रियेच्या गुळगुळीतपणावर आणि कट पृष्ठभागाच्या सपाटपणावर परिणाम करते. खराब दर्जाच्या ब्लेडमुळे घर्षण आणि थर्मल ताण वाढतो, ज्यामुळे क्रॅक किंवा चिप्स होण्याची शक्यता असते. योग्य ब्लेड मटेरियल निवडणे अत्यंत महत्वाचे आहे. -शीतलक कामगिरी: कूलंट कटिंग तापमान कमी करण्यास, घर्षण कमी करण्यास आणि कचरा साफ करण्यास मदत करतात. अप्रभावी कूलंटमुळे उच्च तापमान आणि कचरा जमा होऊ शकतो, ज्यामुळे कटिंगची गुणवत्ता आणि कार्यक्षमता प्रभावित होते. कार्यक्षम आणि पर्यावरणपूरक कूलंट निवडणे अत्यंत महत्वाचे आहे. | ब्लेडची गुणवत्ता कटच्या अचूकतेवर आणि गुळगुळीतपणावर परिणाम करते. कुचकामी शीतलकामुळे कटिंगची गुणवत्ता आणि कार्यक्षमता कमी होऊ शकते, ज्यामुळे शीतलकाचा इष्टतम वापर करण्याची आवश्यकता अधोरेखित होते. |
प्रक्रिया नियंत्रण आणि गुणवत्ता तपासणी | -प्रक्रिया नियंत्रण: कटिंग प्रक्रियेत स्थिरता आणि सातत्य सुनिश्चित करण्यासाठी प्रमुख कटिंग पॅरामीटर्सचे रिअल-टाइम निरीक्षण आणि समायोजन. -गुणवत्ता तपासणी: कापणीनंतरच्या देखावा तपासणी, परिमाणात्मक मोजमाप आणि विद्युत कामगिरी चाचणी गुणवत्तेच्या समस्या त्वरित ओळखण्यास आणि त्यांचे निराकरण करण्यास मदत करते, ज्यामुळे कटिंगची अचूकता आणि सुसंगतता सुधारते. | योग्य प्रक्रिया नियंत्रण आणि गुणवत्ता तपासणीमुळे सातत्यपूर्ण, उच्च-गुणवत्तेचे कटिंग परिणाम आणि संभाव्य समस्या लवकर ओळखण्यास मदत होते. |

कटिंगची गुणवत्ता सुधारणे
कटिंगची गुणवत्ता सुधारण्यासाठी प्रक्रिया पॅरामीटर्स, उपकरणे आणि साहित्य निवड, प्रक्रिया नियंत्रण आणि तपासणी यांचा विचार करून एक व्यापक दृष्टिकोन आवश्यक आहे. कटिंग तंत्रज्ञानाचे सतत परिष्करण करून आणि प्रक्रिया पद्धती ऑप्टिमाइझ करून, वेफर कटिंगची अचूकता आणि स्थिरता आणखी वाढवता येते, ज्यामुळे सेमीकंडक्टर उत्पादन उद्योगाला अधिक विश्वासार्ह तांत्रिक आधार मिळतो.
#०३ कटिंगनंतर हाताळणी आणि चाचणी
३.१ स्वच्छता आणि वाळवणे
चिपची गुणवत्ता आणि त्यानंतरच्या प्रक्रियांची सुरळीत प्रगती सुनिश्चित करण्यासाठी वेफर कटिंग नंतर साफसफाई आणि वाळवण्याचे टप्पे महत्त्वाचे आहेत. या टप्प्यात, कटिंग दरम्यान निर्माण होणारे सिलिकॉन कचरा, शीतलक अवशेष आणि इतर दूषित घटक पूर्णपणे काढून टाकणे आवश्यक आहे. साफसफाई प्रक्रियेदरम्यान चिप्स खराब होणार नाहीत याची खात्री करणे देखील तितकेच महत्वाचे आहे आणि वाळवल्यानंतर, गंज किंवा इलेक्ट्रोस्टॅटिक डिस्चार्ज सारख्या समस्या टाळण्यासाठी चिपच्या पृष्ठभागावर ओलावा राहणार नाही याची खात्री करा.
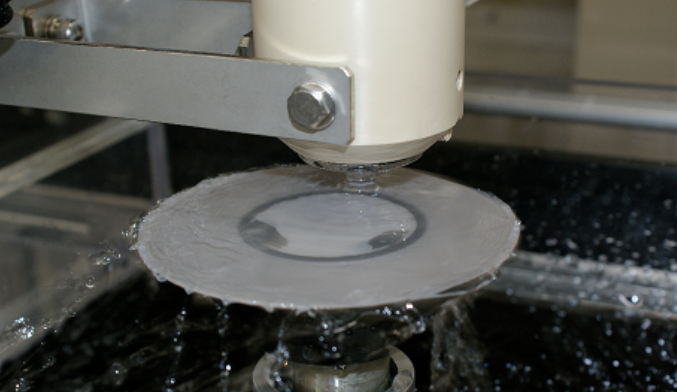
कापणीनंतरची हाताळणी: साफसफाई आणि वाळवण्याची प्रक्रिया
प्रक्रिया पायरी | सामग्री | प्रभाव |
साफसफाईची प्रक्रिया | -पद्धत: स्वच्छतेसाठी विशेष स्वच्छता एजंट आणि शुद्ध पाणी वापरा, अल्ट्रासोनिक किंवा यांत्रिक ब्रशिंग तंत्रांसह. | दूषित पदार्थ पूर्णपणे काढून टाकण्याची खात्री करते आणि साफसफाई दरम्यान चिप्सचे नुकसान टाळते. |
-स्वच्छता एजंटची निवड: चिपला नुकसान न करता प्रभावी साफसफाई सुनिश्चित करण्यासाठी वेफर मटेरियल आणि दूषित पदार्थांच्या प्रकारानुसार निवडा. | प्रभावी स्वच्छता आणि चिप संरक्षणासाठी योग्य एजंट निवड ही गुरुकिल्ली आहे. | |
-पॅरामीटर नियंत्रण: अयोग्य साफसफाईमुळे होणाऱ्या गुणवत्तेच्या समस्या टाळण्यासाठी साफसफाईचे तापमान, वेळ आणि साफसफाईच्या द्रावणाचे प्रमाण काटेकोरपणे नियंत्रित करा. | नियंत्रणे वेफरचे नुकसान टाळण्यास किंवा दूषित पदार्थ मागे ठेवण्यास मदत करतात, ज्यामुळे सातत्यपूर्ण गुणवत्ता सुनिश्चित होते. | |
वाळवण्याची प्रक्रिया | -पारंपारिक पद्धती: नैसर्गिक हवेत वाळवणे आणि गरम हवेत वाळवणे, ज्यांची कार्यक्षमता कमी असते आणि त्यामुळे स्थिर वीज जमा होऊ शकते. | यामुळे सुकण्याचा वेळ कमी होऊ शकतो आणि संभाव्य स्थिर समस्या येऊ शकतात. |
-आधुनिक तंत्रज्ञान: चिप्स लवकर सुकतील आणि हानिकारक परिणाम टाळतील यासाठी व्हॅक्यूम ड्रायिंग आणि इन्फ्रारेड ड्रायिंग सारख्या प्रगत तंत्रज्ञानाचा वापर करा. | जलद आणि अधिक कार्यक्षम वाळवण्याची प्रक्रिया, स्थिर डिस्चार्ज किंवा ओलावा-संबंधित समस्यांचा धोका कमी करते. | |
उपकरणांची निवड आणि देखभाल | -उपकरणांची निवड: उच्च-कार्यक्षमता असलेली साफसफाई आणि वाळवण्याची यंत्रे प्रक्रिया कार्यक्षमता सुधारतात आणि हाताळणी दरम्यान संभाव्य समस्यांवर बारकाईने नियंत्रण ठेवतात. | उच्च-गुणवत्तेची मशीन्स चांगली प्रक्रिया सुनिश्चित करतात आणि साफसफाई आणि वाळवताना चुका होण्याची शक्यता कमी करतात. |
-उपकरणांची देखभाल: उपकरणांची नियमित तपासणी आणि देखभाल केल्याने ते चांगल्या स्थितीत राहते आणि चिपच्या गुणवत्तेची हमी मिळते. | योग्य देखभालीमुळे उपकरणांचे बिघाड टाळता येतो, ज्यामुळे विश्वासार्ह आणि उच्च-गुणवत्तेची प्रक्रिया सुनिश्चित होते. |
कापणीनंतरची स्वच्छता आणि वाळवणे
वेफर कटिंग नंतर साफसफाई आणि वाळवण्याचे टप्पे ही गुंतागुंतीची आणि नाजूक प्रक्रिया आहेत ज्यासाठी अंतिम प्रक्रिया परिणाम सुनिश्चित करण्यासाठी अनेक घटकांचा काळजीपूर्वक विचार करणे आवश्यक आहे. वैज्ञानिक पद्धती आणि कठोर प्रक्रिया वापरून, प्रत्येक चिप नंतरच्या पॅकेजिंग आणि चाचणी टप्प्यात चांगल्या स्थितीत प्रवेश करेल याची खात्री करणे शक्य आहे.
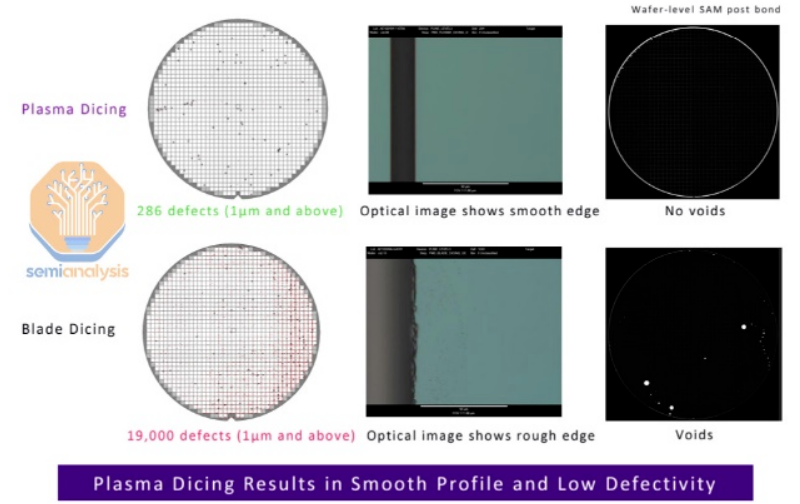
कापणीनंतरची तपासणी आणि चाचणी
पाऊल | सामग्री | प्रभाव |
तपासणी पायरी | १.दृश्य तपासणी: चिपच्या पृष्ठभागावर भेगा, चिपिंग किंवा दूषितता यासारखे दृश्यमान दोष तपासण्यासाठी दृश्यमान किंवा स्वयंचलित तपासणी उपकरणे वापरा. कचरा टाळण्यासाठी शारीरिकदृष्ट्या खराब झालेले चिप्स त्वरित ओळखा. | प्रक्रियेच्या सुरुवातीलाच दोषपूर्ण चिप्स ओळखण्यास आणि काढून टाकण्यास मदत करते, ज्यामुळे साहित्याचे नुकसान कमी होते. |
२.आकार मोजमाप: चिपचे परिमाण अचूकपणे मोजण्यासाठी अचूक मापन यंत्रे वापरा, कट आकार डिझाइन वैशिष्ट्यांशी जुळतो याची खात्री करा आणि कामगिरीच्या समस्या किंवा पॅकेजिंग अडचणी टाळा. | चिप्स आवश्यक आकार मर्यादेत आहेत याची खात्री करते, ज्यामुळे कामगिरीतील घट किंवा असेंब्ली समस्या टाळता येतात. | |
३.विद्युत कामगिरी चाचणी: नॉन-कॉम्प्लायंट चिप्स ओळखण्यासाठी आणि केवळ कार्यप्रदर्शन-पात्र चिप्स पुढील टप्प्यावर जाण्याची खात्री करण्यासाठी, प्रतिरोध, कॅपेसिटन्स आणि इंडक्टन्स यासारख्या प्रमुख विद्युत पॅरामीटर्सचे मूल्यांकन करा. | प्रक्रियेत फक्त कार्यात्मक आणि कार्यक्षमता-चाचणी केलेल्या चिप्स पुढे जातील याची खात्री करते, ज्यामुळे नंतरच्या टप्प्यात अपयशाचा धोका कमी होतो. | |
चाचणी चरण | १.कार्यात्मक चाचणी: चिपची मूलभूत कार्यक्षमता अपेक्षिततेनुसार कार्य करते याची पडताळणी करा, कार्यात्मक असामान्यता असलेल्या चिप्स ओळखा आणि काढून टाका. | नंतरच्या टप्प्यात जाण्यापूर्वी चिप्स मूलभूत ऑपरेशनल आवश्यकता पूर्ण करतात याची खात्री करते. |
२.विश्वसनीयता चाचणी: दीर्घकाळ वापरात किंवा कठोर वातावरणात चिप कामगिरी स्थिरतेचे मूल्यांकन करा, ज्यामध्ये सामान्यत: उच्च-तापमान वृद्धत्व, कमी-तापमान चाचणी आणि आर्द्रता चाचणी यांचा समावेश असतो जेणेकरून वास्तविक-जगातील अत्यंत परिस्थितींचे अनुकरण करता येईल. | विविध पर्यावरणीय परिस्थितीत चिप्स विश्वसनीयरित्या कार्य करू शकतात याची खात्री करते, ज्यामुळे उत्पादनाचे दीर्घायुष्य आणि स्थिरता सुधारते. | |
३.सुसंगतता चाचणी: चिप इतर घटकांसह किंवा सिस्टीमसह योग्यरित्या कार्य करते याची पडताळणी करा, विसंगतीमुळे कोणतेही दोष किंवा कार्यक्षमतेत घट होत नाही याची खात्री करा. | सुसंगतता समस्या टाळून वास्तविक जगातील अनुप्रयोगांमध्ये सुरळीत ऑपरेशन सुनिश्चित करते. |
३.३ पॅकेजिंग आणि स्टोरेज
वेफर कटिंगनंतर, चिप्स हे सेमीकंडक्टर उत्पादन प्रक्रियेतील एक महत्त्वाचे उत्पादन आहे आणि त्यांचे पॅकेजिंग आणि स्टोरेज टप्पे देखील तितकेच महत्त्वाचे आहेत. योग्य पॅकेजिंग आणि स्टोरेज उपाय केवळ वाहतूक आणि स्टोरेज दरम्यान चिप्सची सुरक्षितता आणि स्थिरता सुनिश्चित करण्यासाठीच नव्हे तर त्यानंतरच्या उत्पादन, चाचणी आणि पॅकेजिंग टप्प्यांसाठी मजबूत आधार प्रदान करण्यासाठी देखील आवश्यक आहेत.
तपासणी आणि चाचणी टप्प्यांचा सारांश:
वेफर कटिंगनंतर चिप्ससाठी तपासणी आणि चाचणी चरणांमध्ये दृश्य तपासणी, आकार मोजमाप, विद्युत कामगिरी चाचणी, कार्यात्मक चाचणी, विश्वसनीयता चाचणी आणि सुसंगतता चाचणी यासह अनेक पैलूंचा समावेश आहे. हे चरण एकमेकांशी जोडलेले आणि पूरक आहेत, उत्पादनाची गुणवत्ता आणि विश्वासार्हता सुनिश्चित करण्यासाठी एक ठोस अडथळा निर्माण करतात. कठोर तपासणी आणि चाचणी प्रक्रियेद्वारे, संभाव्य समस्या ओळखल्या जाऊ शकतात आणि त्वरित सोडवल्या जाऊ शकतात, ज्यामुळे अंतिम उत्पादन ग्राहकांच्या गरजा आणि अपेक्षा पूर्ण करते याची खात्री होते.
पैलू | सामग्री |
पॅकेजिंग उपाय | १.अँटी-स्टॅटिक: पॅकेजिंग मटेरियलमध्ये उत्कृष्ट अँटी-स्टॅटिक गुणधर्म असले पाहिजेत जेणेकरून स्टॅटिक वीज उपकरणांना नुकसान पोहोचवू नये किंवा त्यांच्या कार्यक्षमतेवर परिणाम करू नये. |
२.ओलावा प्रतिरोधक: पॅकेजिंग साहित्यांमध्ये आर्द्रतेचा प्रतिकार चांगला असावा जेणेकरून आर्द्रतेमुळे होणारा गंज आणि विद्युत कार्यक्षमतेचा बिघाड रोखता येईल. | |
३.शॉकप्रूफ: पॅकेजिंग मटेरियलने प्रभावी शॉक शोषण प्रदान केले पाहिजे जेणेकरून वाहतुकीदरम्यान चिप्सचे कंपन आणि आघातांपासून संरक्षण होईल. | |
स्टोरेज वातावरण | १.आर्द्रता नियंत्रण: जास्त आर्द्रतेमुळे होणारे ओलावा शोषण आणि गंज किंवा कमी आर्द्रतेमुळे होणाऱ्या स्थिर समस्या टाळण्यासाठी योग्य मर्यादेत आर्द्रता काटेकोरपणे नियंत्रित करा. |
२.स्वच्छता: धूळ आणि अशुद्धतेमुळे चिप्स दूषित होऊ नयेत म्हणून स्वच्छ साठवणूक वातावरण ठेवा. | |
३.तापमान नियंत्रण: कमी तापमानामुळे जास्त उष्णता किंवा संक्षेपण समस्यांमुळे होणारे जलद वृद्धत्व टाळण्यासाठी वाजवी तापमान श्रेणी सेट करा आणि तापमान स्थिरता राखा. | |
नियमित तपासणी | वेळेवर संभाव्य समस्या ओळखण्यासाठी आणि त्यांचे निराकरण करण्यासाठी दृश्य तपासणी, आकार मोजमाप आणि विद्युत कामगिरी चाचण्या वापरून साठवलेल्या चिप्सची नियमितपणे तपासणी आणि मूल्यांकन करा. साठवणुकीचा वेळ आणि परिस्थितीनुसार, चिप्सचा वापर चांगल्या स्थितीत केला जाईल याची खात्री करण्यासाठी त्यांचे नियोजन करा. |
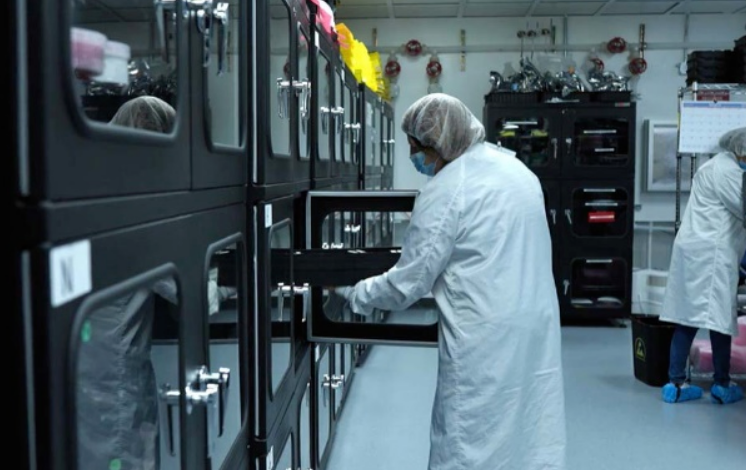
वेफर डायसिंग प्रक्रियेदरम्यान सूक्ष्म क्रॅक आणि नुकसान ही समस्या सेमीकंडक्टर उत्पादनात एक महत्त्वाची आव्हान आहे. कटिंग स्ट्रेस हे या घटनेचे प्राथमिक कारण आहे, कारण त्यामुळे वेफर पृष्ठभागावर लहान क्रॅक आणि नुकसान होते, ज्यामुळे उत्पादन खर्च वाढतो आणि उत्पादनाची गुणवत्ता कमी होते.
या आव्हानाला तोंड देण्यासाठी, कटिंगचा ताण कमी करणे आणि ऑप्टिमाइझ्ड कटिंग तंत्रे, साधने आणि परिस्थिती लागू करणे अत्यंत महत्त्वाचे आहे. ब्लेड मटेरियल, कटिंग स्पीड, प्रेशर आणि कूलिंग पद्धती यासारख्या घटकांकडे काळजीपूर्वक लक्ष दिल्यास मायक्रोक्रॅकची निर्मिती कमी होण्यास आणि प्रक्रियेचे एकूण उत्पादन सुधारण्यास मदत होऊ शकते. याव्यतिरिक्त, लेसर डायसिंगसारख्या अधिक प्रगत कटिंग तंत्रज्ञानामध्ये चालू असलेले संशोधन या समस्या आणखी कमी करण्याचे मार्ग शोधत आहे.
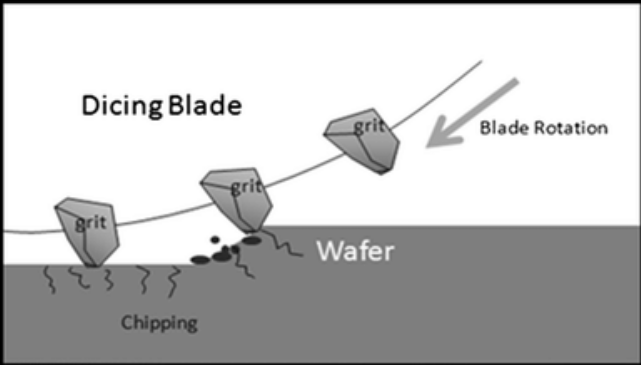
नाजूक पदार्थ असल्याने, वेफर्समध्ये यांत्रिक, थर्मल किंवा रासायनिक ताण आल्यावर अंतर्गत संरचनात्मक बदल होतात, ज्यामुळे सूक्ष्म क्रॅक तयार होतात. जरी या क्रॅक लगेच लक्षात येत नसल्या तरी, उत्पादन प्रक्रिया पुढे सरकत असताना त्या विस्तारू शकतात आणि अधिक गंभीर नुकसान करू शकतात. ही समस्या नंतरच्या पॅकेजिंग आणि चाचणी टप्प्यांमध्ये विशेषतः समस्याप्रधान बनते, जिथे तापमानातील चढउतार आणि अतिरिक्त यांत्रिक ताणांमुळे हे सूक्ष्म क्रॅक दृश्यमान फ्रॅक्चरमध्ये विकसित होऊ शकतात, ज्यामुळे चिप बिघाड होण्याची शक्यता असते.
हा धोका कमी करण्यासाठी, कटिंग गती, दाब आणि तापमान यासारख्या पॅरामीटर्सचे ऑप्टिमायझेशन करून कटिंग प्रक्रियेचे काळजीपूर्वक नियंत्रण करणे आवश्यक आहे. लेसर डायसिंगसारख्या कमी आक्रमक कटिंग पद्धती वापरल्याने वेफरवरील यांत्रिक ताण कमी होऊ शकतो आणि मायक्रोक्रॅकची निर्मिती कमी होऊ शकते. याव्यतिरिक्त, वेफर डायसिंग प्रक्रियेदरम्यान इन्फ्रारेड स्कॅनिंग किंवा एक्स-रे इमेजिंग सारख्या प्रगत तपासणी पद्धती लागू केल्याने या सुरुवातीच्या टप्प्यातील क्रॅक अधिक नुकसान होण्यापूर्वी शोधण्यात मदत होऊ शकते.
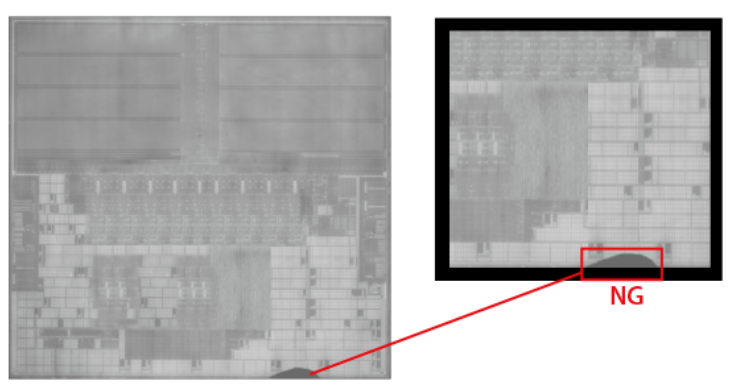
डायसिंग प्रक्रियेत वेफर पृष्ठभागाचे नुकसान ही एक महत्त्वाची चिंता आहे, कारण त्याचा थेट परिणाम चिपच्या कामगिरीवर आणि विश्वासार्हतेवर होऊ शकतो. असे नुकसान कटिंग टूल्सचा अयोग्य वापर, चुकीचे कटिंग पॅरामीटर्स किंवा वेफरमध्येच अंतर्निहित असलेल्या मटेरियल दोषांमुळे होऊ शकते. कारण काहीही असो, या नुकसानीमुळे सर्किटच्या विद्युत प्रतिकारात किंवा कॅपेसिटन्समध्ये बदल होऊ शकतात, ज्यामुळे एकूण कामगिरीवर परिणाम होतो.
या समस्यांचे निराकरण करण्यासाठी, दोन प्रमुख धोरणांचा शोध घेतला जात आहे:
१. कटिंग टूल्स आणि पॅरामीटर्स ऑप्टिमायझ करणे: धारदार ब्लेड वापरून, कटिंगचा वेग समायोजित करून आणि कटिंगची खोली बदलून, कटिंग प्रक्रियेदरम्यान ताणाचे प्रमाण कमी करता येते, त्यामुळे नुकसान होण्याची शक्यता कमी होते.
२. नवीन कटिंग तंत्रज्ञानाचा शोध घेणे: लेसर कटिंग आणि प्लाझ्मा कटिंग सारख्या प्रगत तंत्रांमुळे वेफरला होणाऱ्या नुकसानाची पातळी कमी करताना सुधारित अचूकता मिळते. वेफरवरील थर्मल आणि यांत्रिक ताण कमी करून उच्च कटिंग अचूकता मिळविण्याचे मार्ग शोधण्यासाठी या तंत्रज्ञानाचा अभ्यास केला जात आहे.
थर्मल इम्पॅक्ट एरिया आणि त्याचे कामगिरीवर होणारे परिणाम
लेसर आणि प्लाझ्मा कटिंग सारख्या थर्मल कटिंग प्रक्रियेत, उच्च तापमान अपरिहार्यपणे वेफरच्या पृष्ठभागावर थर्मल इम्पॅक्ट झोन तयार करते. हे क्षेत्र, जिथे तापमान ग्रेडियंट महत्त्वपूर्ण आहे, ते सामग्रीच्या गुणधर्मांमध्ये बदल करू शकते, ज्यामुळे चिपच्या अंतिम कामगिरीवर परिणाम होतो.
औष्णिक प्रभावित क्षेत्राचा (TAZ) परिणाम:
क्रिस्टल रचनेत बदल: उच्च तापमानात, वेफर मटेरियलमधील अणूंची पुनर्रचना होऊ शकते, ज्यामुळे क्रिस्टल रचनेत विकृती निर्माण होते. ही विकृती मटेरियलला कमकुवत करते, त्याची यांत्रिक शक्ती आणि स्थिरता कमी करते, ज्यामुळे वापरादरम्यान चिप बिघाड होण्याचा धोका वाढतो.
विद्युत गुणधर्मांमधील बदल: उच्च तापमानामुळे सेमीकंडक्टर पदार्थांमधील वाहक एकाग्रता आणि गतिशीलता बदलू शकते, ज्यामुळे चिपची विद्युत चालकता आणि विद्युत प्रवाह प्रसारण कार्यक्षमता प्रभावित होते. या बदलांमुळे चिपच्या कार्यक्षमतेत घट होऊ शकते, ज्यामुळे ते त्याच्या हेतूसाठी अयोग्य बनू शकते.
या परिणामांना कमी करण्यासाठी, कटिंग दरम्यान तापमान नियंत्रित करणे, कटिंग पॅरामीटर्स ऑप्टिमाइझ करणे आणि कूलिंग जेट्स किंवा पोस्ट-प्रोसेसिंग ट्रीटमेंट्स सारख्या पद्धतींचा शोध घेणे हे थर्मल इफेक्टची व्याप्ती कमी करण्यासाठी आणि सामग्रीची अखंडता राखण्यासाठी आवश्यक धोरणे आहेत.
एकंदरीत, वेफर डायसिंग तंत्रज्ञानामध्ये मायक्रोक्रॅक्स आणि थर्मल इम्पॅक्ट झोन दोन्ही महत्त्वाचे आव्हान आहेत. सेमीकंडक्टर उत्पादनांची गुणवत्ता सुधारण्यासाठी आणि त्यांची बाजारातील स्पर्धात्मकता वाढविण्यासाठी तांत्रिक प्रगती आणि गुणवत्ता नियंत्रण उपायांसह सतत संशोधन आवश्यक असेल.
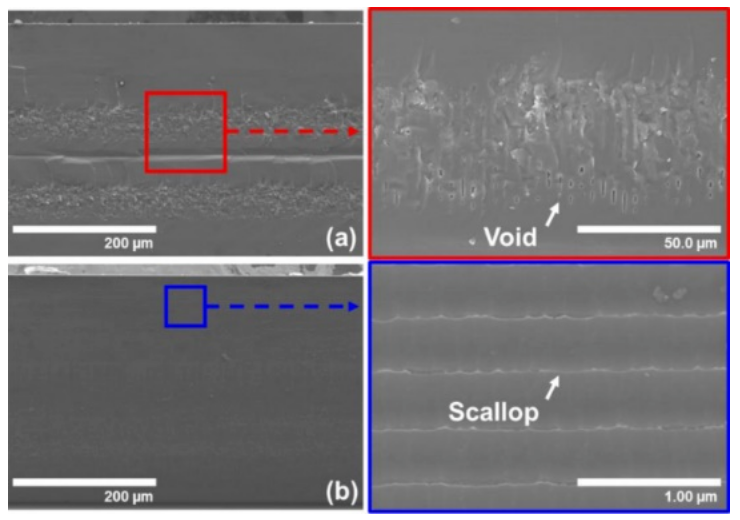
थर्मल इम्पॅक्ट झोन नियंत्रित करण्यासाठी उपाय:
कटिंग प्रक्रियेचे पॅरामीटर्स ऑप्टिमायझ करणे: कटिंग स्पीड आणि पॉवर कमी केल्याने थर्मल इम्पॅक्ट झोन (TAZ) चा आकार प्रभावीपणे कमी करता येतो. हे कटिंग प्रक्रियेदरम्यान निर्माण होणाऱ्या उष्णतेचे प्रमाण नियंत्रित करण्यास मदत करते, ज्याचा थेट परिणाम वेफरच्या मटेरियल गुणधर्मांवर होतो.
प्रगत शीतकरण तंत्रज्ञान: द्रव नायट्रोजन कूलिंग आणि मायक्रोफ्लुइडिक कूलिंग सारख्या तंत्रज्ञानाचा वापर थर्मल इम्पॅक्ट झोनची श्रेणी लक्षणीयरीत्या मर्यादित करू शकतो. या कूलिंग पद्धती उष्णता अधिक कार्यक्षमतेने नष्ट करण्यास मदत करतात, अशा प्रकारे वेफरचे भौतिक गुणधर्म जपतात आणि थर्मल नुकसान कमी करतात.
साहित्य निवड: संशोधक कार्बन नॅनोट्यूब आणि ग्राफीन सारख्या नवीन पदार्थांचा शोध घेत आहेत, ज्यात उत्कृष्ट थर्मल चालकता आणि यांत्रिक शक्ती आहे. हे पदार्थ चिप्सची एकूण कार्यक्षमता सुधारताना थर्मल इम्पॅक्ट झोन कमी करू शकतात.
थोडक्यात, जरी थर्मल इम्पॅक्ट झोन हा थर्मल कटिंग तंत्रज्ञानाचा अपरिहार्य परिणाम असला तरी, ऑप्टिमाइझ्ड प्रोसेसिंग तंत्रे आणि मटेरियल निवडीद्वारे ते प्रभावीपणे नियंत्रित केले जाऊ शकते. भविष्यातील संशोधन अधिक कार्यक्षम आणि अचूक वेफर डायसिंग साध्य करण्यासाठी थर्मल कटिंग प्रक्रियांचे फाइन-ट्यूनिंग आणि ऑटोमेशनवर लक्ष केंद्रित करेल.

शिल्लक धोरण:
वेफर डायसिंग तंत्रज्ञानामध्ये वेफर उत्पन्न आणि उत्पादन कार्यक्षमता यांच्यातील इष्टतम संतुलन साधणे हे एक सततचे आव्हान आहे. उत्पादकांना तर्कसंगत उत्पादन धोरण आणि प्रक्रिया मापदंड विकसित करण्यासाठी बाजारातील मागणी, उत्पादन खर्च आणि उत्पादन गुणवत्ता यासारख्या अनेक घटकांचा विचार करावा लागतो. त्याच वेळी, उत्पादन कार्यक्षमता वाढवताना उत्पादन राखण्यासाठी किंवा सुधारण्यासाठी प्रगत कटिंग उपकरणे सादर करणे, ऑपरेटर कौशल्ये सुधारणे आणि कच्च्या मालाचे गुणवत्ता नियंत्रण वाढवणे आवश्यक आहे.
भविष्यातील आव्हाने आणि संधी:
सेमीकंडक्टर तंत्रज्ञानाच्या प्रगतीसह, वेफर कटिंगला नवीन आव्हाने आणि संधींचा सामना करावा लागतो. चिपचा आकार कमी होत असताना आणि एकत्रीकरण वाढत असताना, कटिंगची अचूकता आणि गुणवत्तेची मागणी लक्षणीयरीत्या वाढते. त्याच वेळी, उदयोन्मुख तंत्रज्ञान वेफर कटिंग तंत्रांच्या विकासासाठी नवीन कल्पना प्रदान करतात. उत्पादकांनी बाजारातील गतिशीलता आणि तांत्रिक ट्रेंडशी जुळवून घेतले पाहिजे, बाजारातील बदल आणि तांत्रिक मागण्या पूर्ण करण्यासाठी उत्पादन धोरणे आणि प्रक्रिया पॅरामीटर्स सतत समायोजित आणि ऑप्टिमायझ केले पाहिजेत.
शेवटी, बाजारातील मागणी, उत्पादन खर्च आणि उत्पादनाची गुणवत्ता या बाबींचा एकत्रित विचार करून आणि प्रगत उपकरणे आणि तंत्रज्ञान सादर करून, ऑपरेटर कौशल्ये वाढवून आणि कच्च्या मालाचे नियंत्रण मजबूत करून, उत्पादक वेफर डायसिंग दरम्यान वेफर उत्पन्न आणि उत्पादन कार्यक्षमतेमध्ये सर्वोत्तम संतुलन साधू शकतात, ज्यामुळे कार्यक्षम आणि उच्च-गुणवत्तेचे अर्धसंवाहक उत्पादन उत्पादन होते.
भविष्यातील दृष्टीकोन:
जलद तांत्रिक प्रगतीसह, सेमीकंडक्टर तंत्रज्ञान अभूतपूर्व वेगाने प्रगती करत आहे. सेमीकंडक्टर उत्पादनातील एक महत्त्वाचा टप्पा म्हणून, वेफर कटिंग तंत्रज्ञान रोमांचक नवीन विकासासाठी सज्ज आहे. भविष्याकडे पाहता, वेफर कटिंग तंत्रज्ञानामुळे अचूकता, कार्यक्षमता आणि खर्चात लक्षणीय सुधारणा होण्याची अपेक्षा आहे, ज्यामुळे सेमीकंडक्टर उद्योगाच्या सतत वाढीमध्ये नवीन चैतन्य येईल.
वाढत्या अचूकता:
उच्च अचूकतेच्या शोधात, वेफर कटिंग तंत्रज्ञान विद्यमान प्रक्रियांच्या मर्यादा सतत ओलांडत राहील. कटिंग प्रक्रियेच्या भौतिक आणि रासायनिक यंत्रणेचा सखोल अभ्यास करून आणि कटिंग पॅरामीटर्सचे अचूक नियंत्रण करून, वाढत्या जटिल सर्किट डिझाइन आवश्यकता पूर्ण करण्यासाठी बारीक कटिंग परिणाम साध्य केले जातील. याव्यतिरिक्त, नवीन साहित्य आणि कटिंग पद्धतींचा शोध घेतल्याने उत्पादन आणि गुणवत्तेत लक्षणीय सुधारणा होईल.
कार्यक्षमता वाढवणे:
नवीन वेफर कटिंग उपकरणे स्मार्ट आणि ऑटोमेटेड डिझाइनवर लक्ष केंद्रित करतील. प्रगत नियंत्रण प्रणाली आणि अल्गोरिदमच्या परिचयामुळे उपकरणे वेगवेगळ्या साहित्य आणि डिझाइन आवश्यकता पूर्ण करण्यासाठी कटिंग पॅरामीटर्स स्वयंचलितपणे समायोजित करण्यास सक्षम होतील, ज्यामुळे उत्पादन कार्यक्षमता लक्षणीयरीत्या सुधारेल. मल्टी-वेफर कटिंग तंत्रज्ञान आणि जलद ब्लेड रिप्लेसमेंट सिस्टम यासारख्या नवोपक्रम कार्यक्षमता वाढविण्यात महत्त्वपूर्ण भूमिका बजावतील.
खर्च कमी करणे:
वेफर कटिंग तंत्रज्ञानाच्या विकासासाठी खर्च कमी करणे ही एक महत्त्वाची दिशा आहे. नवीन साहित्य आणि कटिंग पद्धती विकसित होत असताना, उपकरणांचा खर्च आणि देखभाल खर्च प्रभावीपणे नियंत्रित होण्याची अपेक्षा आहे. याव्यतिरिक्त, उत्पादन प्रक्रिया ऑप्टिमायझेशन आणि स्क्रॅप दर कमी केल्याने उत्पादनादरम्यान कचरा आणखी कमी होईल, ज्यामुळे एकूण उत्पादन खर्च कमी होईल.
स्मार्ट मॅन्युफॅक्चरिंग आणि आयओटी:
स्मार्ट मॅन्युफॅक्चरिंग आणि इंटरनेट ऑफ थिंग्ज (IoT) तंत्रज्ञानाचे एकत्रीकरण वेफर कटिंग तंत्रज्ञानात परिवर्तनात्मक बदल घडवून आणेल. डिव्हाइसेसमधील इंटरकनेक्टिव्हिटी आणि डेटा शेअरिंगद्वारे, उत्पादन प्रक्रियेच्या प्रत्येक टप्प्याचे रिअल टाइममध्ये निरीक्षण आणि ऑप्टिमाइझ केले जाऊ शकते. हे केवळ उत्पादन कार्यक्षमता आणि उत्पादनाची गुणवत्ता सुधारत नाही तर कंपन्यांना अधिक अचूक बाजार अंदाज आणि निर्णय घेण्यास समर्थन देखील प्रदान करते.
भविष्यात, वेफर कटिंग तंत्रज्ञान अचूकता, कार्यक्षमता आणि खर्चात उल्लेखनीय प्रगती करेल. या प्रगतीमुळे सेमीकंडक्टर उद्योगाचा सतत विकास होईल आणि मानवी समाजात अधिक तांत्रिक नवकल्पना आणि सुविधा येतील.
पोस्ट वेळ: नोव्हेंबर-१९-२०२४